Not just concrete! Grout can be similar, but is tailored especially for masonry
Masonry construction is used for all kinds of loadbearing applications, ranging from relatively simple single storey structures to more complex multi-storey buildings in seismic zones. An important component of masonry assemblages is the grout, which can be required to increase the fire resistance rating or axial load-carrying capacity of masonry, or bond reinforcing bars to the surrounding block, allowing them to act together in resisting loads.
Many designers and specification writers are more familiar with concrete construction and as a result, commonly use concrete specifications for masonry grout. This is incorrect and should be avoided to ensure compliance with CSA masonry standards. While the basic materials of masonry grout are the same as concrete (aggregate, cement, water), the environment, purpose, and pouring conditions are vastly different. As a result, masonry grout requires material properties that are very different than what would be desirable for concrete.
Masonry grout can be specified using two different paths of compliance within CSA A179-14: Mortar and grout for unit masonry: proportion specification, or property specification.
A common mistake when specifying masonry grout is not understanding the differences that are associated with masonry grout in comparison to grout used for other applications. The purpose of this article is to explain the differences and offer insight on how grout can be specified to comply with the CSA Masonry standards and provide suitable structural performance.
Part of our Masonry Specification Series
Offering recommendations accompanied with background explanatory material to explain how these recommendations were formed. Click here to see the full series.
Disclaimer
The information contained here is intended to serve as educational content for designers, specifiers, or contractors. It is not to be relied upon for formal technical advice, as masonry projects may have details and considerations that are unique to a particular project and may be beyond the scope of the content of this page.
Recommendations
Masonry grout is different than concrete or grouts used in other aspects of construction. Masonry grouts should be specified under the requirements for either proportion or property specifications in accordance with CSA A179-14: Mortar and grout for masonry. High strength requirements should be avoided, and a high slump is required. For the vast majority of designs where masonry assemblage strengths are taken from CSA S304-14: Table 4, there is no need to specify a higher grout strength, regardless of the block strength used. Generally, indicating in the specification that the grout (fine grout or coarse grout) must meet the proportion specification requirements of CSA A179-14 is sufficient without specifying a minimum strength.
Discussion
Proportion or Property specified grouts – both are acceptable!
Masonry grout must meet the requirements of CSA A179-14: Mortar and grout for unit masonry. Under this standard there are two separate compliance paths to specify grout: proportion specifications and property specifications. Proportion specified grout is for jobsite mixing where CSA approved materials are to be mixed to the volume-based proportions given in Table 5 of the Standard. Property specified grouts allow for manufacturers to use innovative materials to enhance the properties or behaviour of masonry grout but must follow strict testing requirements to ensure acceptable performance.
Allowable aggregate sizes and gradations
Aggregate sizes for masonry grouts do not typically match the acceptable gradations for concrete. Aggregates for concrete are typically coarser and harsher compared to aggregates for masonry grout. Most aggregate suppliers will therefore carry ‘mortar sand’ or ‘masonry sand’ to allow for the batching of CSA-compliant masonry grouts. Additionally, the aggregate gradations are also different between fine and course grouts. Gradation requirements for aggregates in masonry grouts are found in Table 1 of CSA A179-14 Mortar and grout for unit masonry.
Both grout types are suitable for masonry construction, but each has its own advantages. A coarse grout will require less cement per volume, and it is generally a less expensive alternative to fine grout, while fine grout is required in heavily reinforced or otherwise congested masonry. For instance, when both vertical and horizontal reinforcement are present, especially at lap splice locations, a fine grout can better facilitate a complete bond between the grout, reinforcement, and masonry units, while reducing the probability of voids.
Depending on the unit size and reinforcement configuration, fine grout may be required to satisfy minimum reinforcement clearances within the masonry unit cell, as covered within CSA A371-14 Masonry construction:
8.2.5.7.1 Clear Distance
The clear distance between the surface of a bar and any surface of a masonry unit shall be not less than 6 mm for fine grout and 13 mm for coarse grout. Cross-webs of hollow or semi-solid units may be used as support for horizontal reinforcement.
CSA A371
This is one case where the CSA standards call for one particular grout type. So long as a grout meets all other provisions within CSA A179 through either compliance pathway, the masonry contractor can opt to use either fine or coarse and expect satisfactory results.
Strength requirements – not always necessary
There are no minimum strength requirements for proportion specified grouts, because they have a proven record of performance through past experience and decades of research.
Masonry assemblage design strengths found in CSA S304-14, Table 4 are based on proportion specified grouts. Proportion specified grouts will typically test to a minimum compressive strength of 10 to 12 MPa at 28 days when cast in non-absorbent cylinder molds. However, once again, there is no minimum strength required if the grout is mixed to the correct proportion specification.
The minimum 28-day compressive strengths for property specified grouts are 10 MPa and 12.5 MPa, for fine and coarse grout, respectively. Designers familiar with concrete construction, or with grout products in general, may think that this strength is low. However, the compressive strength of grout used in masonry construction is affected by its consistency at the time of pouring, by the size of the voids it will need to fill, and by the level of absorption of the masonry units in contact with the grout.
The following key properties differentiate masonry grouts from traditional concrete:
High slump is needed for proper placement
Masonry grout must be fluid enough to fill all voids within the masonry cells and fully encapsulate the reinforcement, which requires a grout with high slump (required between 200 mm and 275 mm) and consequently a high water-to-cement ratio.
Excess water is absorbed once it is placed
A high water-to-cement ratio is also necessary to help replace the moisture absorbed by the surrounding masonry. Grouts are not “cast” into a non-absorbent form, they are poured into masonry units that are absorbent and will draw free water from the grout.
Strength in the cylinder does not reflect strength in the wall
The compressive strength of grout cylinders does not provide a realistic comparison to the in-situ conditions. A grout cylinder is cast in a non-absorbent mold, whereas the in-situ pouring of grout is into the cells of concrete masonry units. These are not the same conditions for curing. The masonry units absorb some of the moisture from the grout reducing the water-to-cement ratio, and hence increasing the in-situ actual compressive strength of the grout. This absorption process also plays an important part in providing a strong bond between the grout and the masonry units.
Guidance on this difference is available in CSA S304-14 Design of masonry structures:
12.4.1.2
In lieu of more detailed determination of the in-situ grout strength, the value of f’gr in Clause 12.4 shall be taken as 1.5 times the 28 d grout cylinder strength determined in accordance with the test method in CSA A179.
Note: For grout in accordance with the proportion specification of CSA A179, a typical value assumed for the in-situ strength of f’gr is 20 MPa. The strength of in-situ grout is higher than the strength of cylinders cast in non-absorbent moulds because suction by the masonry units reduces the water content of the grout.
CSA A371
For masonry design, the in-situ compressive strength of grout can be estimated as 1.5 times the 28-day grout cylinder strength, or roughly taken simply as 20 MPa for proportion specified grout, unless a more detailed determination of the in-situ grout strength is provided.
Diminishing returns on any increases in grout strength
The other factor to consider with these “low” grout strengths is that higher grout strengths show very minimal increase in the strength of the masonry assemblage. An experimental program conducted by Drysdale and Hamid[1] showed a minimal increase in assemblage strength (solid line) when grout was increased from 15 MPa to 45 MPa.
This increase was much lower than the increase in strength that would be expected by adding the strength of the grout in the grouted area to the strength of the ungrouted prism (dotted line):
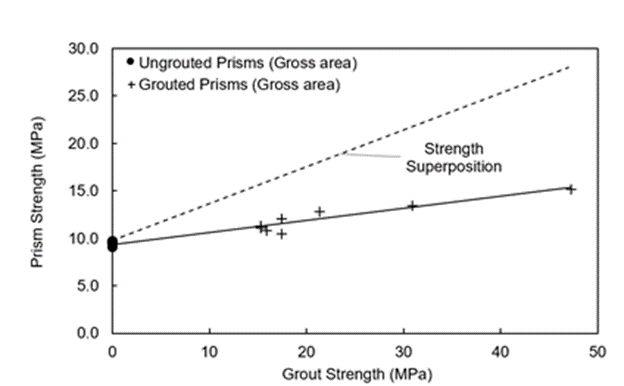
While it might be tempting to specify a stronger grout to match the strength of the masonry unit, decades of testing and experience have shown diminishing returns with higher grout strengths. The compressive strengths that engineers rely upon for their design calculations take the relatively low strength and high slump into account and can be seen in CSA S304-14: Table 4, Note (4).
Cylinder tests as low as 10 MPa for a proportion specified grout are compliant for use with even 30 MPa specified unit strengths. It is far more important that the grout be workable and fill all voids, bonding reinforcement to the units, than have a higher strength with a lower slump at the time of pouring.
Notes:
[1] R. G. Drysdale and A. A. Hamid, “Behaviour of Concrete Block Masonry under Axial Compression”, ACI Journal, Vol. 76, No. 6, 1979, pp. 707-721.
A high slump is the most important material property
The required slump of grout for unit masonry is between 200 mm and 275 mm and is typically achieved by mixing grout with a high water-to-cement ratio (reducing the cylinder strength of the grout). High strength and high slump grouts are possible with the use of plasticizers or water reducing agents; however, these materials can increase the viscosity of the grout to a point where it will “stick” to mortar fins and unit webs creating voids within the wall. Plasticizers can be effectively used, but it is recommended that the use of plasticizers is limited to property specified grouts with a proven track record of performance and reliability rather than adding plasticizer on the jobsite to achieve a certain slump. The inside of the cells of unit masonry can be quite congested; mortar fins, rebar can be in multiple direction (especially a concern at lap splices), offset webs from course to course, flares in the unit webs and face shells, etc. Due to this congestion, the most important property of a masonry grout is the flowability to ensure there are no voids. Mixing enough water to facilitate a slump around 275 mm will allow for adequate grout placement without needing any plasticizers.
Caution regarding specifying non-shrink masonry grout for standard masonry applications
Masonry grouts meeting the proportion specification of CSA A179, using conventional materials and procedures, have a proven record of performance. They have the properties required for grout in new masonry construction.
However, some have believed that non-shrink or expansive grout can improve the properties of masonry construction and as a result, certain manufacturers have therefore taken to producing pre-blended property specified grouts with expansive agents to decrease shrinkage. Although it is possible for grouts which comply with the performance specification requirements of CSA A179-14 to contain an expansive agent, the manufacturer of such a product must still demonstrate that it meets all requirements of the standard. No benefit to the masonry assemblage, from the use of non-shrink or expansive grout, should be assumed without verification through assemblage testing, provided by the manufacturer, and approved to the satisfaction of the designer. Designers are reminded, that the testing performed for the determination of the strength and durability properties of masonry assemblages as part of the development of CSA standards has been conducted using a conventional proportion-specified grout (without any additives, plasticizers, or expansive agents).
While each manufacture’s product will differ, caution is required when specifying a proprietary non-shink grout mix and it is critical that the specified mix be intended for use in masonry construction. Certain types of non-shrink grouts, not intended for masonry, are mixed to a very low or no slump, have very low water-to-cement ratios, and do not meet the requirements of CSA A179. Non-shrink grout products are often used for highly localized applications, such as under bearing surfaces such as base plates. Any proprietary product intended for a specialized application, and for which each manufacturer provides guidelines through their own specification, should be understood by the designer and the contractor prior to its use.
Return to Recommendations section. Return to the Specifications page.
Part of our Masonry Specification Series
Offering recommendations accompanied with background explanatory material to explain how these recommendations were formed. Click here to see the full series.
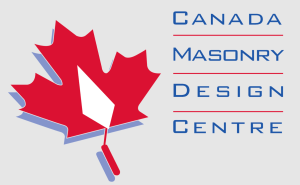
Have a question about anything here?
CMDC is made up of offices across Canada, connecting you with support through our team of technical staff.
Providing clarity and raising issues before they turn into real problems
As part of our overall effort to educate the design community and our contractor members, CMDC has compiled a collection of articles meant to address common areas of misunderstanding or confusion that have resulted in issues in past projects.